High-pressure Gas ProductsProducts
High-pressure
Gas Products
High-pressure Gas Vessels
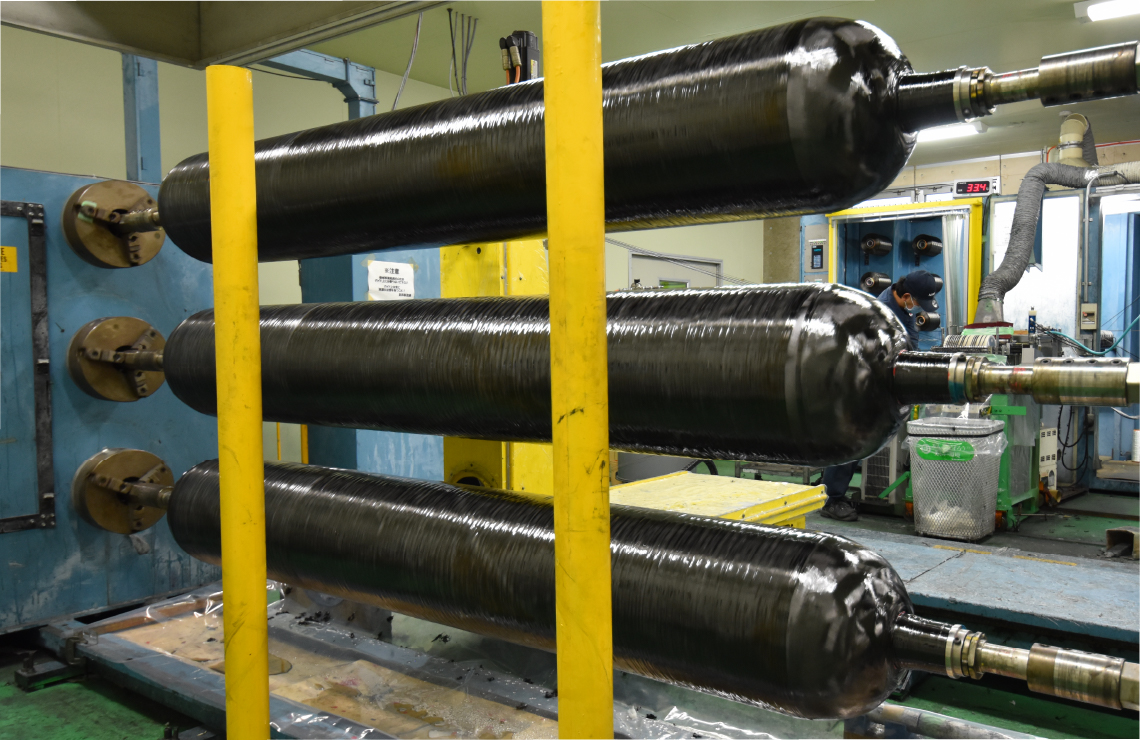
Development of and initiatives
for hydrogen gas vessels
for hydrogen gas vessels
The Type III high-pressure composite container, which is manufactured using an ultra-light aluminum liner (aluminum container) manufactured using a unique design system and filament winding (carbon fiber CFRP wrapping process), is used in hydrogen station filling equipment, compression We provide innovative solutions in a wide variety of fields, including hydrogen storage and transport containers, space exploration, and small containers for air breathing apparatus.
Through the development and manufacture of high-pressure composite containers, we are promoting the spread of hydrogen energy and helping build a clean energy future. We are always deeply pursuing safety, lightness, and low cost, and continue to take on the challenge of developing products for the next future.
Equipment

Filament-winding machine
Equipment name | Number of lines |
---|---|
Eddy current testing equipment | 1 |
Bore grinder | 1 |
Large spinning machine | 1 |
Bend measuring device | 1 |
Filament-winding machine | 2 |
Curing furnaces (large, medium, small) | 3 |
Hydro-testing machines (large, small) | 2 |
Cycle-testing pressure intensifiers (large, small) |
2 |
Burst tester | 1 |
Airtightness tester | 4 |

-
Iwatani Hydrogen Station
in Kofu -
STN Tokushima
Mobile Hydrogen Station
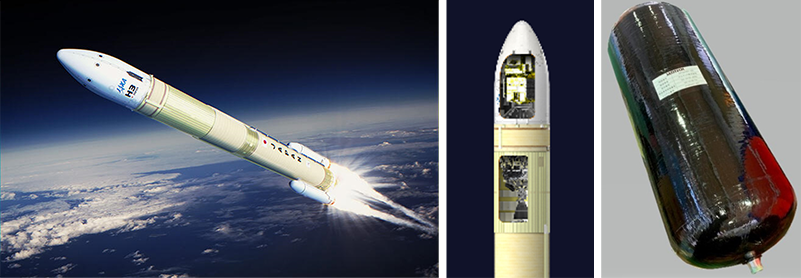
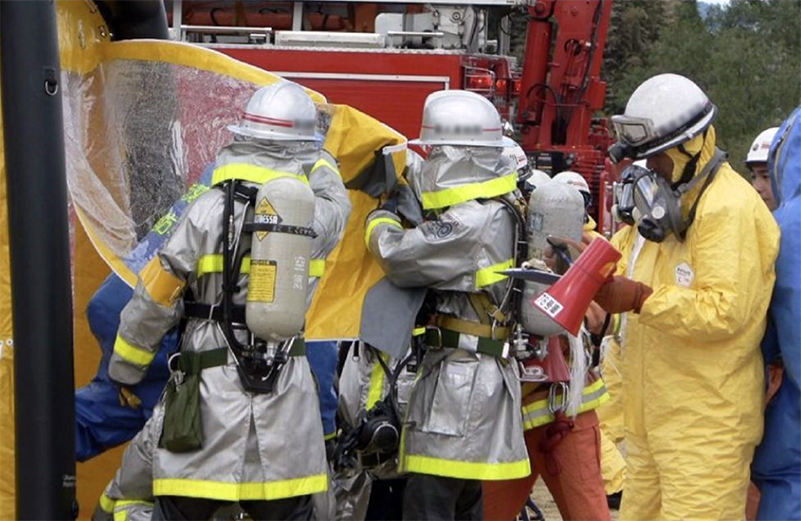
Performance testing service for high voltage equipment
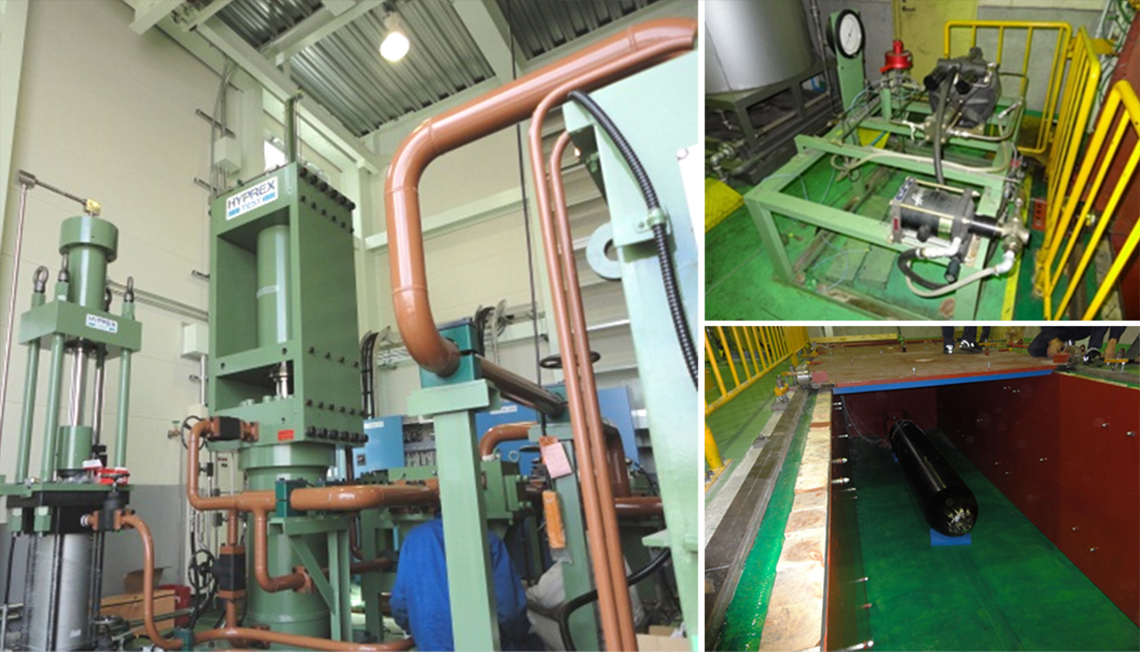
We undertake airtightness (leakage) tests, room temperature pressure cycle tests, burst tests, etc. for pressure vessel products and their materials.
In order to build strong partnerships with our customers, we hold detailed discussions regarding test methods and test conditions. All customer information entrusted to us will be kept strictly confidential and will not be leaked to any other company. Protecting your confidential information is our top priority.
We also flexibly respond to customer requests, such as issuing inspection reports regarding test results and taking photos of test conditions. The main testing methods we carry out are shown below.
- Airtightness test(Leakage)
- The airtightness of the specimen is checked by filling the specimen with gas (nitrogen/helium) at a specified pressure and holding it for a certain period of time.
- Burst testing
- Pressure (water) is applied to the specimen, the pressure at the time of rupture is measured, and the condition of the ruptured specimen is confirmed.
- Normal temperature pressure frequency test
- The specified pressure (water) (upper limit pressure/lower limit pressure) is repeatedly applied to the test specimen, and the pressure is increased or decreased until leakage occurs from the test specimen or the specified number of times.
Contact information:
High-pressure Gas Vessel Division,
SAMTECH Corporation,
SAMTECH Corporation,
1452-7 Komagaya, Hanabikino, Osaka, 583-0841
Phone: +81-72-977-8801
Fax: +81-72-977-8802
Email: vessel@samtech.co.jp